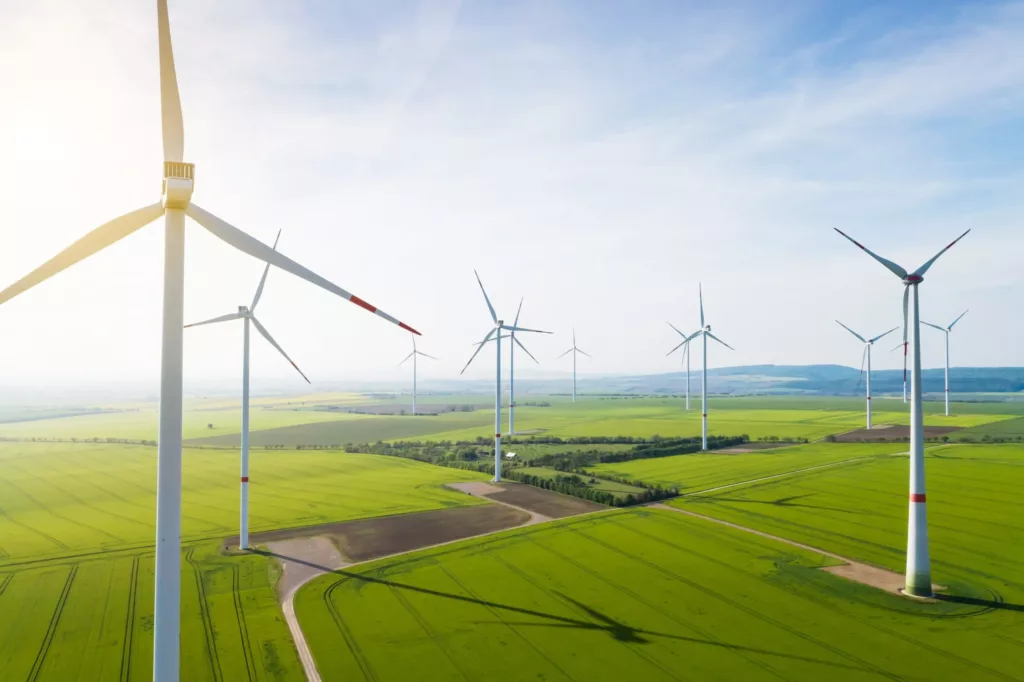
IDENTIFIED FAILURES
INDUSTRY
- Renewable Energy
ASSET
- Wind Turbine
PROBLEM
- Cable Joint damage
AVOIDED
- Unplanned Stoppage
- Loss of production
THE ROLE OF WIND TURBINES IN ENERGY PRODUCTION
Wind turbines are essential in the global transition to sustainable energy. By converting wind into electricity, they offer a clean, renewable alternative to fossil fuels with no direct carbon emissions. Advances in turbine technology have made wind power more efficient and affordable, helping decarbonize the energy sector. As countries aim to reduce fuel imports and diversify energy sources, wind energy strengthens energy security, supports economic stability, and promotes environmental sustainability.
IMPORTANCE OF CABLES CONNECTING THE WIND TURBINE TO THE SUBSTATION
Cables linking wind turbines to substations are crucial for transporting generated electricity to the grid. These components must endure environmental stress, mechanical loads, and voltage fluctuations. Their quality and condition affect energy efficiency, operational safety, and overall system reliability. Proper cable design, insulation and maintenance help to avoid faults and ensure long-term performance of wind energy systems.
CONSEQUENCES OF CABLE FAILURES
Cable failures can disrupt power transmission, causing energy losses and financial setbacks. These failures are especially costly due to the complexity of repairs and limited access. Persistent or unnoticed damage can lead to overheating, system faults and further component failures, reducing lifespan and safety. Extended downtimes may also affect grid reliability and investor trust, underscoring the importance of durable cables, continuous monitoring, and preventive maintenance.